Code EK000119
3 layers Adtech Provera Cast Line
ADTECH PROVERA
CAST FILM EXTRUSION MACHINES
The 3 layer Adtech Provera Cast Film Line HWR 1000/3 model allow to produce stretch wrap film with high quality winding. This stretch film extrusion machine gives to customers efficient stretch film production capability with a film width of 1 mt and an output rate of up to 600 kg/h. Completely automatic, suitable for manual and automatic rolls.
Technical Data | |||
---|---|---|---|
REFERENCE MACHINE | HWR 1000/3 | ||
MATERIALS | LDPE, LLDPE | ||
FILM WIDTH (MAX) | 1.000 mm | ||
NUMBER OF EXTRUDERS | 3 | ||
THICKNESS RANGE | 6 µm | ||
FILM THICKNESS (MAX) | 70 µm | ||
NUMBER OF LAYERS | 3 | ||
NET OUTPUT (MAX) | 600 Kg/h | ||
PRODUCTION FILM WIDTH | 2 x 500 mm | ||
EXTRUSION FLAT DIE | AUTOFLEX VI WITH IN-DIE FEEDBLOCK (EDI) |
Cast Film Extrusion Machines
The Cast film Extrusion lines are used to extrude plastic films for flexible packaging industry.
Typically, the cast film process involves the use of co-extrusion, which is a simultaneous extrusion of two or more materials from a single die to form a multi-layered film. This is because in many cases the final application of the plastic film demands a performance that cannot be achieved if the film is composed of only one material.
Cast film extrusion lines designed for stretch film extrude mainly linear low density polyethylene (LLDPE) in blends with other polymers and additives. CPP co-extrusion lines extrude polypropylene (PP) in various blends and multilayer structures. Barrier film structures involve also EVOH and nylon (PA), which adds barrier properties to film.
In the cast film extrusion process, the molten polymer travels through a flat die system to adopt its final flat film shape. The die system is formed by the die and feedblock (if the process requires coextrusion) or simply the die, if the process is that of mono-layer extrusion. The process starts with the feeding of plastic resins by means of a gravimetric feeding system to one or more extruders. The materials are then melted and mixed by the extruders, filtered and fed to the die system. Immediately after exiting the die, the molten curtain enters the cooling unit where its temperature is lowered with a water cooled chill roll to “freeze” the film. The film is then passed downstream where the edges are trimmed and the film is wound into rolls.
Co-extruded films typically contain up to seven layers; however, the use of more layers is becoming more common. The number of layers, their position in the coextrudate and their individual thickness are all variables that change depending on the particular application of the film. Such multi-layer film solutions are of enormous advantage in optimising packaging performance, functionality and cost because they combine the properties of the different components in a synergistic way.
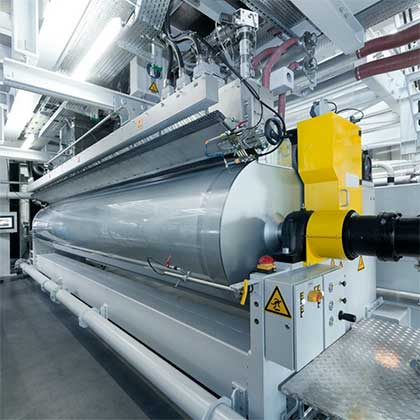