Code EK000391
Double Wire Paper Machine Carcano
CARCANO
PAPER MAKING PLANT
This used double wire paper making plant machine produced by Carcano has been designed to manufacture brown paper for containerboard with a grammage from 115 gsm to 200 gsm.
This Second-Hand paper machine allow high productions with a range up designed to 720 m/min and a trimmed paper width of 4.640 mm.
Technical Data | |||
---|---|---|---|
REFERENCE MACHINE | 4640 DOUBLE WIRE FOURDRINIER | ||
ITEM | BROWN PAPER FOR CONTAINERBOARD | ||
RATION | 115 - 200 g/m2 | ||
OPERATING SPEED | up to 720 m/min | ||
MAX DRIVE SPEED | 750 m/min | ||
DESIGN SPEED DRYER SECTION | 1.000 m/min | ||
MAX SALEABLE WIDTH AFTER REWINDER | 4.640 mm | ||
LIST OF EQUIPMENT | HIGH DENSITY CYCLON COARSE SCREENING COARSE SCREENING FINE SCEENING (BOTOM PLY) FINE SCEENING (BOTOM PLY) FINE SCEENING (TOP PLY) FINE SCEENING (TOP PLY) THICKENER AUGERS REFINERS | ||
SLITTER WINDER | MAX. PARENT ROLL DIAMETER 2.700 mm MAX. TRIMMED WIDTH PARENT ROLL 5.300 mm MAX. OPERATING SPEED 2.500 m/min MAX. ROLL DIAMETER 1.500 mm CUSTOMER REEL WIDTH 700 – 2.800 mm MAX. CUSTOMER REEL WEIGHT 3.000 Kg |
Paper Machines
A Paper Machine is used in the Pulp and Paper industry to create paper in large quantities at high speed.
Modern Paper Machines are based on the principles of the Fourdrinier Machine, which uses a moving woven mesh to create a continuous paper web by filtering out the fibres held in a paper stock and producing a continuously moving wet mat of fibre.
This is dried in the machine to produce a strong paper web.
Paper machines have at least six distinct operational sections:
Forming section: is a continuous rotating wire mesh which removes water from the paper.
Press section: where the wet fibre web passes between large rolls loaded under high pressure to squeeze out as much water as possible.
Drying section: where the pressed sheet passes in a serpentine manner, a series of steam heated drying cylinders. Drying removes the water content down to a level of about 6%, where it will remain at typical indoor atmospheric conditions.
Size Press section: where the semi-dried paper is applied with a thin layer of starch and/ or other chemicals to improve several paper properties.
Calender section: where the dried paper is smoothened under high loading and pressure and so it shrinks through the drying section and is held in tension between the press section and the calender.
Reel section: where paper coming out of the machine is wound onto individual spools for further processing.
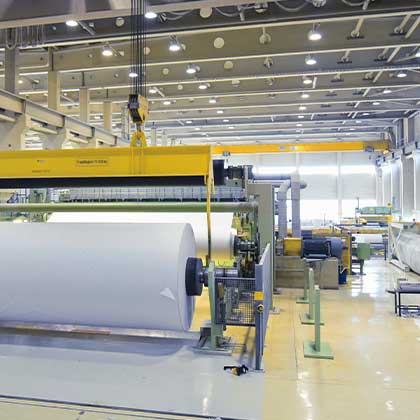