Code EK000190
3-Layers DMT 6800 BOPP film line
DMT
BOPP BOPET PACKAGING FILM EXTRUSION LINES
This 3-layer co-extruded BOPP film extrusion line produced by DMT is used for the production of many BOPP film types for a wide variety of applications. DMT has developed high output lines for top quality film production.
This Second-hand 3-Layers DMT 6800 BOPP film machine allow a range up to 2.800 kg/h and a film width of 6.800 mm.
Technical Data | |||
---|---|---|---|
REFERENCE MACHINE | BI-ORIENTED DMT 6800 | ||
MATERIALS | BOPP | ||
FILM WIDTH (MAX) | 6.800 mm | ||
NUMBER OF EXTRUDERS | 3 (CO-EXTRUDERS A/B/C) | ||
NUMBER OF LAYERS | 3 | ||
FILM THICKNESS RANGE | from 15 µm to 60 µm | ||
NET OUTPUT (MAX) | 2.800 Kg/h | ||
MAX MECHANICAL SPEED | 350 mt/min | ||
MDO | 14 PRE-HEATING ROLLS - ELECTRICAL HEATERS; 4 STRETCHING ROLLS - CIRCULATING OIL; 2 ANNEALING ROLLS - ELECTRICAL HEATERS; 5 NIP ROLLS; AC DRIVE; STRETCHING RATIO 1:1 - 1:6 | ||
TDO | CHAIN AND CHAIN TRACK SYSTEM; HEATING SYSTEM: CIRCULATING AIR VIA INDIVIDUAL HEATING SYSTEM / ZONE (ELECTRICAL HEATER, MOTORS, FANS, SENSOR, ETC) EDGE GUIDE SYSTEM AT INLET |
BOPP/BOPET Extrusion Lines
BOPP (Biaxially oriented polypropylene) and BOPET (Biaxially oriented polyester) films are the most common supports used in the food packaging and printing. BOPET is more stable through printing and laminating processes than BOPP and is often preferred where high-quality graphics are required.
These plastic films are produced in tender-frame lines where the material (PP or PET) is melted through a flat extrusion die (T-die) and solidified onto a cooled roller. The material is then stretched in the machine direction in an MDO and then in the transverse direction in a TDO. Solid-phase orientation processes create very significant changes in film properties that can be quite valuable in packaging structures. These changes permit films that are lighter weight and thinner than standard blown or cast films to satisfy performance needs by generating significant increases in such properties as tensile strength, toughness, heat stability, tear initiation resistance, and barrier.
Both BOPP and PET films can be produced in a variety of thicknesses, making them suitable for different types of packaging applications. Various types of finishes, such as matte, glossy and metallic, are also achievable, allowing manufacturers to create packaging with different textures and visual effects. With the growing demand for individual packaging, BOPP and PET films are likely to remain popular choices for manufacturers looking to create high-quality custom packaging that protects their products and enhances their brand image.
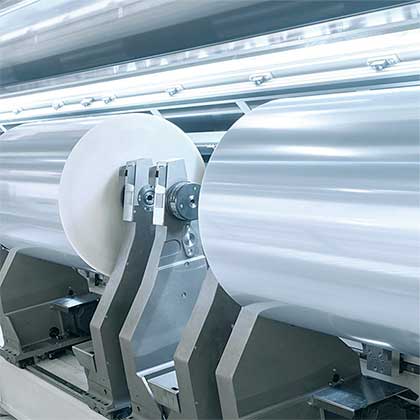