Code EK000162
1100 Kentya PET Sheet Extrusion Film Line
KENTYA
SHEET EXTRUSION MACHINES
The Kentya 1100 PET Sheet Extrusion Film Line allow to produce foils and sheets in every kind of plastic material. This second-hand Sheet Extrusion Film Machine Twin Screw model gives to customers versatile sheets film production capability with a film width of 1.100 mm and an output rate of up to 500 kg/h.
The change of the rollers is very rapid.
Technical Data | |||
---|---|---|---|
REFERENCE MACHINE | PET Sheet 82 | ||
MATERIALS | PET | ||
FILM WIDTH (MAX) |
1.100 mm
| ||
NUMBER OF EXTRUDERS | 2 | ||
NET OUTPUT (MAX) | 500 Kg/h | ||
DIE | 1.100 mm | ||
NUMBER OF LAYERS | 2/3 | ||
CALENDAR | 1.100 mm | ||
MAIN EXTRUDER SCREW DIAMETER | 65 mm 33 L/D Single Screw Extruder | ||
COROTATING TWIN SCREW EXTRUDER | 82 mm 40 L/D | ||
HAUL OFF WINDER | 1.100 mm | ||
WINDER | 1.100 mm Servo Controlled Winder Dual Station
|
Sheet Extrusion Machines
The sheet extrusion is a common process to extrude plastic sheets or films that are too thick to be blown. In Particular, plastic granules including additives, are fed from the extruder hopper along a heated cylinder by a rotating screw, melted & homogenized and conveyed to the sheet die.
There are two types of dies used: T-shaped and coat hanger. The purpose of these dies is to reorient and guide the flow of polymer melt from a single round output from the extruder to a thin, flat planar flow.
Depending on the application, there are a number of variations including the number and rotation of the screws, the screw and cylinder geometry and the structure. The die itself can be fed by several extruders extruding different thermoplastics, resulting in layered or concentric co-extrudates. The extrudate is then cooled via chill rolls and transported to slitting and winding stations.In sheet extrusion, these cooling rolls not only deliver the necessary cooling but also determine sheet thickness and surface texture.
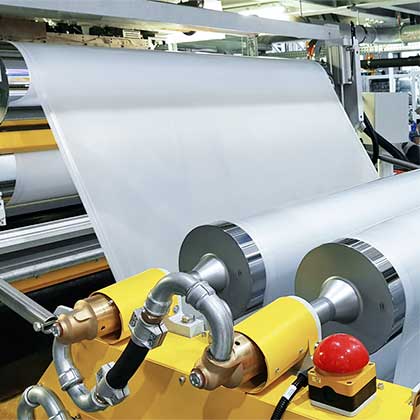
Main Applications:
Printing and Converting
Food Packaging
Waterproofing