Code EK000179
W&H Primaflex CL 8 CI Flexo Press
WINDMÖLLER & HÖLSCHER
CI FLEXO
PRINTING MACHINES
This used Windmöller & Hölscher Primaflex CL 8 CI Flexographic Printing Press allow high and stable print quality with a range up to 400 m/min and a film width till of 1.270 mm.
W&H stands for innovation and trailblazing technologies in modern flexography. The CI flexo presses produced are designed for a wide range of applications offering the highest print quality and output. Primaflex model offers unique solutions for all of customers needs in flexible packaging printing.
Technical Data | |||
---|---|---|---|
REFERENCE MACHINE | PRIMAFLEX CL 8 | ||
NUMBER OF COLORS | 8 | ||
GEARLESS | YES | ||
PRINTING WIDTH | 1.270 mm | ||
WEB WIDTH | 1.320 mm | ||
MECHANICAL SPEED | 400 m/min | ||
PRINT REPEAT RANGE | min 370 mm / max 1.070 mm | ||
FILM THICKNESS RANGE | from 20 μm to 150 μm (LDPE, PP), from 12 μm to 100 μm (HDPE, OPP), from 10 μm to 30 μm (PET, OPA, BOPP), from 30 to 120 g/m2 (PAPER) |
Flexo CI
Flexographic printing machine is a method which uses a flexible relief plate to print onto a substrate. It is essentially a modern version of letterpress, evolved with high speed rotary functionality, which can be used for printing on almost any type of substrate, including plastic, metallic films, cellophane, and paper.
Today's flexo printing presses use photopolymer printing plates containing a mirror relief image of the required print. The raised areas on the plate have ink applied to them by an anilox roller and then transfer it onto the substrate.
Flexo CI presses use a central drum which is common to all colours as counter impression roll.
In a modern flexographic press, each print unit comprises of Anilox roller, Chambered doctor blade system, Plate cylinder, Impression cylinder, Inking system.
In the print units, driers may be installed so that subsequent colors can be applied to the substrate without merging into those previously printed. These driers may utilize hot air, infra red or ultra-violet light, depending on the application.
Basically, During the printing process, the ink is pumped into the ink chamber of the doctor blade system. Two blades within the ink chamber, the barrier blade and the doctor blade, seal either end and confine the ink to the chamber while it is in contact with the anilox roller. As the anilox roller rotates, the cells in contact with the doctor blade system collect ink, and then any surface excess is removed as the roller passes under the doctor blade. As the anilox rotates, its surface comes into contact with the raised areas of the printing plates mounted on the plate cylinder, transferring the ink. The printing plate then rotates and transfers the image onto the substrate.
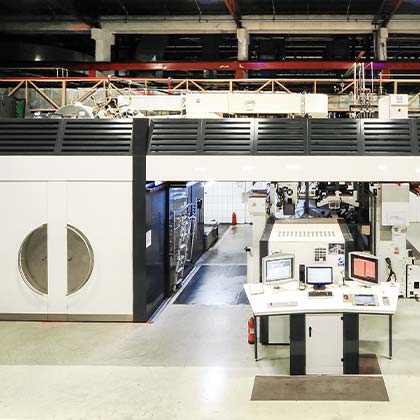