Code EK000224
3 layers Rajoo 2200 Blown Film Extrusion Line
RAJOO
BLOWN FILM EXTRUSION LINES
The Rajoo 3 layers Blown Film Machine MULTIFOIL RECF-2360-75/2200 IBC-A-Three Layers model is a compact line for a top quality film production with a range up to 400 kg/h and a film width of 2.200 mm. This production line of 3 layers co-extrusion blown film extruder produced by RAJOO can be used for the production of a wide range of general packaging films as it allows to achieve a high output and a significant level of productivity and flexibility.
Technical Data | |||
---|---|---|---|
REFERENCE MACHINE | MULTIFOIL RECF-2360-75/2200 IBC-A-Three Layers | ||
MATERIALS | LDPE, LLDPE | ||
FILM WIDTH (MAX) | 2.200 mm | ||
NUMBER OF EXTRUDERS | 3 | ||
THICKNESS RANGE | from 20 µm to 150 µm | ||
FILM STRUCTURE | A - B - C | ||
GAP | 2,2 mm | ||
STANDARD DIE DIAMETER | 450 mm | ||
EXTRUDER COMBINATION | 60.32D / 60.32D / 75.32D | ||
NET OUTPUT (MAX) | 400 Kg/h | ||
MECHANICAL LINE SPEED | 100 mt/min |
Blown Film Extrusion Machines
The Blown film extrusion lines are used to extrude plastic films for flexible packaging industry.
The process begin commonly through the melt of the granulates into an extruder and pushed through a circular die modeling it in the form of a tube. Subsequently This tube is carefully inflated and simultaneously cooled in its interior and on the exterior surface through the use of an air ring. A set of collapsing guides are then used to collapse the bubble into two, more defined, layers within closer proximity, a series of nip rollers flatten the layers together to form a two-layered plastic film that is then wound onto a cylindrical roll for packaging purposes.
Blown film extrusion is also versatile and able to manufacture a variety of single or multi-layer films with a range of film thickness and width. Raw material most used are low density polyethylene (LDPE) and High density polyethylene (HDPE).
Film produced with this kind of line have most applications from film for bags, to shrink film, lamination film, stretch hoods, PE film for packaging, barrier and many others.
The principal advantages of manufacturing film by this process include the ability to:
- produce tubing (both flat and gussetted) in a single operation;
- adjust the film width and thichness by control of the volume of air in the bubble, the output of the extruder and the speed of the haul-off;
- eliminate end effects such as edge bead trim and non uniform temperature that can result from flat die film extrusion;
- capability of biaxial orientation (allowing uniformity of mechanical properties);
- blown film extrusion can be used for the manufacture of co-extruded, multi-layer films for high barrier applications such as food packaging.
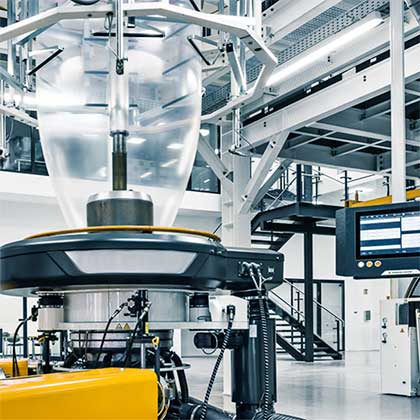